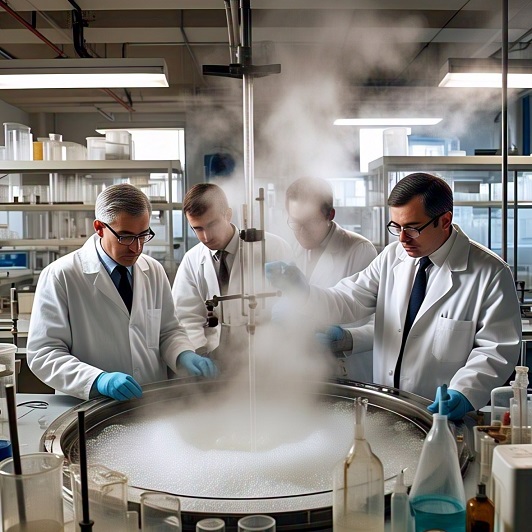
Scientists at the University of Oregon have found a cleaner, electrochemical way to create pure iron metal using saltwater and iron oxide, potentially slashing the carbon footprint of one of the world’s dirtiest industries.
Why Ironmaking Needs a Rethink
Iron is the backbone of global infrastructure. From bridges to buildings and car bodies to cookware, it’s everywhere. Most of it is used in the form of steel, an alloy primarily made by extracting iron from ore, then refining it. However, one major challenge is that producing iron the traditional way is incredibly polluting.
The dominant method still involves blast furnaces, i.e. giant industrial reactors that reach 1,500°C and rely heavily on coal.
Huge Amounts of CO₂
According to the International Energy Agency, the iron and steel industry is responsible for roughly 7 per cent of global CO₂ emissions. In 2024 alone, nearly 2 billion metric tonnes of steel were produced worldwide. In short, in order to make a real impact on cutting carbon emissions, cleaning up steelmaking is essential.
Scientists Develop Electrochemical Route To Iron – No Blast Furnace Required
In answer to this environmental challenge, a team of chemists at the University of Oregon, led by Paul Kempler, have developed an electrochemical process that could reinvent how iron is produced without relying on coal or high-temperature blast furnaces.
Their method uses saltwater and iron oxide, passed through an electrically charged solution to extract pure iron metal. The technique takes place at around 80–90°C, which is far lower than the searing 1,500°C temperatures inside a conventional furnace, and it creates chlorine gas as a useful by-product.
This cleaner process avoids the need for fossil carbon, thereby offering a practical and potentially scalable route to iron production that aligns with global decarbonisation goals.
The Science Behind the Simplicity
The method hinges on passing an electric current through a sodium hydroxide solution containing suspended iron oxide particles. The electrical energy drives a reaction that reduces the iron oxide (Fe₂O₃) into elemental iron (Fe).
This might sound straightforward, but it seems that the real magic lies in the details—specifically, the shape and surface structure of the iron oxide particles.
Postdoctoral researcher Anastasiia Konovalova and graduate student Andrew Goldman discovered that porous, sponge-like particles with a high surface area delivered the best results. These particles dissolved more easily in the solution, speeding up the reaction and producing more iron per square centimetre of electrode.
“With the really porous particles, we can make iron really quickly on a small area,” Goldman said. “The dense particles just can’t achieve the same rate.”
This insight is critical because it addresses one of the biggest barriers to industrial adoption, i.e. cost. Large-scale electrochemical reactors require expensive materials, and their profitability depends on how much product they can generate per unit of electrode area.
The team’s results suggest that with the right materials and conditions, iron could be produced for under $600 per metric tonne, which is actually comparable to conventional blast furnace operations.
Challenges of Scaling Up
While the lab results appear promising, there’s still a long road ahead before electrochemical ironmaking can truly compete with traditional methods at an industrial scale.
For example, a key challenge lies in the raw materials. The researchers saw strong performance using carefully prepared iron oxide powders in controlled settings, but natural iron ores are a different matter. These real-world materials tend to be dense, irregular in shape, and filled with impurities, making them far less suited to the same electrochemical process.
To address this, Kempler’s team is now reported to be developing ways to process lower-grade ores into more porous, high-surface-area forms that mimic the lab-made powders shown to perform best. They’re also collaborating with civil engineers and electrode manufacturers to explore practical applications and tackle the technical challenges of scaling up the system.
The economics behind their so-called “chlor-iron” process are also being put to the test. As well as producing pure iron, the reaction produces chlorine and sodium hydroxide, two valuable industrial chemicals. If these co-products can be captured and used efficiently, it could significantly improve the commercial viability of the method.
Even so, the process still requires considerable upfront investment, and the performance of the electrochemical cells will need to remain consistently high for the financial model to work long term.
Cleaner Steel
If commercialised, the approach developed by Kempler’s team could significantly reduce the carbon intensity of iron and steel production. For countries like the UK, where the future of steelmaking is under scrutiny due to decarbonisation targets, developments like this are more than academic curiosity. For example, this new method could really help in terms of:
– Environmental impact. Electrochemical ironmaking could eliminate fossil fuel combustion, slashing CO₂, sulphur dioxide, and particulate emissions.
– Energy efficiency. Lower operating temperatures mean less energy is required, especially if the electricity comes from renewable sources.
– Industrial compatibility. The chlorine by-product could serve as a feedstock for other chemical industries, potentially creating circular economy benefits.
According to the UK Steel sector, the British steel industry emits around 12 million tonnes of CO₂ annually, which is around 2.7 per cent of the country’s total emissions. A greener iron production method could, therefore, play a key role in the nation’s Net Zero ambitions.
Rethinking Industrial Solutions
Kempler and his team appear to be cautiously optimistic about their discovery and although they acknowledge that there’s still work to be done, they see the breakthrough as part of a bigger move towards sustainability. As graduate researcher Andrew Goldman says: “We haven’t solved all the problems yet, of course,” adding “But I think it’s an example that serves as a starting point for reimagining what solutions can look like. We can still have industry, technology, and medicine—but we can do it in a way that’s clean. And that’s awesome.”
The underlying message here appears to be that innovation doesn’t have to mean compromise. Cleaner industrial systems are possible and they’re already starting to take shape.
Challenges
Critics, however, may point to the practical hurdles of overhauling a centuries-old industry. For example, transitioning to electrochemical systems will require new equipment, re-training, and significant investment, all while competing with cheaper, established blast furnace methods.
Key Questions Still to Be Answered
It seems, therefore, that the next few years will be crucial in determining whether this technology can live up to its potential. For example, some of the key unknowns include:
– Can porous iron oxide feedstocks be manufactured affordably at industrial volumes?
– Will the system perform consistently when using lower-grade ores?
– How will the chlorine by-product be managed safely and profitably?
– Can the process be integrated into existing steel supply chains without major disruption?
Despite the challenges, the University of Oregon’s findings at least appear to have opened the door to a future where steelmaking doesn’t have to come with a climate cost.
What Does This Mean For Your Organisation?
The University of Oregon team’s breakthrough is still in its early stages, but it appears to add real momentum to the growing push for low-carbon iron and steel production. By moving away from blast furnaces and towards electrochemical methods, scientists may be laying the foundations for a cleaner, more circular form of industrial manufacturing, i.e. one that doesn’t rely on burning fossil fuels to function.
For the UK, which is already under pressure to modernise its steel industry and meet legally binding Net Zero targets, this kind of innovation could be important. While Britain’s domestic steel production has declined in recent decades, the sector still supports thousands of jobs and underpins key supply chains in construction, automotive manufacturing, and energy. If electrochemical ironmaking becomes viable at scale, it could offer UK steelmakers a route to both decarbonise and compete globally, especially if paired with renewable electricity and smart use of co-products like chlorine and sodium hydroxide.
There are wider implications too. For technology developers, chemical suppliers, infrastructure planners and even policymakers, this research opens up new territory. It challenges the assumption that heavy industry must always be dirty and carbon-intensive, and invites a broader rethink of what sustainable manufacturing could look like.
That said, none of this is guaranteed. Scaling from lab to factory floor is rarely straightforward. The process still faces major technical, economic and logistical hurdles, and it’s likely to take years, not months, to prove itself in real-world conditions. However, the concept appears to have passed a crucial test i.e., it works. That in itself is no small achievement in a sector that’s notoriously difficult to decarbonise.
What happens next will depend on how quickly researchers, funders, and industrial partners can build on this early promise. If the pace of progress continues, electrochemical ironmaking could become more than just a scientific milestone and could be a real turning point for one of the world’s most polluting industries.